Piston Accumulator Stations are designed to store energy to back up hydraulic systems when a power failure occurs. They include a combination of gas, liquid, and safety valves. In addition to providing a means of improving system response, these devices also help reduce pulsations and oscillations.
Piston accumulators are manufactured according to statutory standards. They can be supplied as a complete set or custom built. All accumulators are fitted with gas valves for nitrogen pre-charge.
Piston accumulator stations provide maximum safety when storing large volumes of oil. Their construction includes a series of gas cylinders and magnetic filtering devices. This allows them to be installed with less external pipelines.
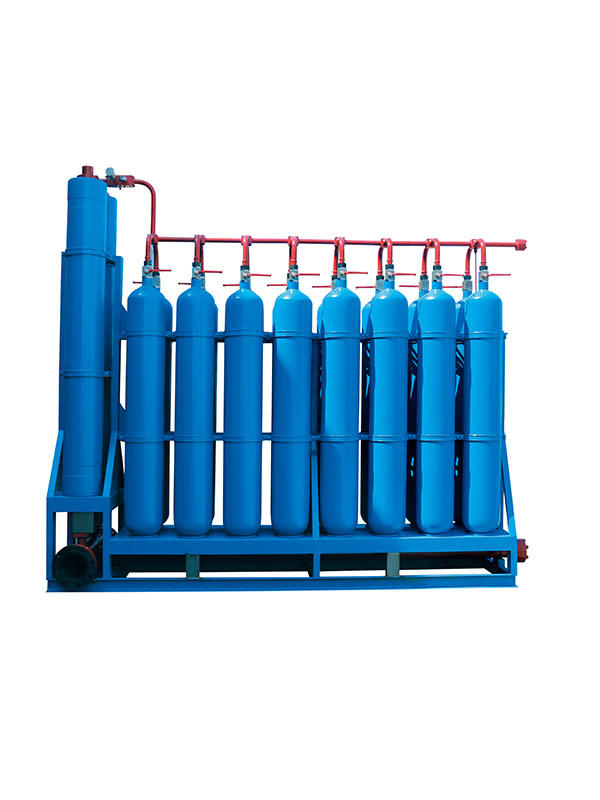
The most common types are bladder, piston, and membrane accumulators. Each has advantages and disadvantages. For instance, bladder accumulators have fewer capacities. However, they are easy to install. These types of accumulators can be designed with multiple cylinders mounted on a common manifold, achieving flows of over 600 gpm.
Piston accumulators are also available in a variety of lengths and sizes. When choosing an accumulator, consider the fluid type, mounting orientation, speed, temperature, and diagnostic characteristics.
In order to keep hydraulic systems working efficiently, users must be aware of how to select an accumulator. For example, the proper selection of a precharge pressure can affect the life of an accumulator. If the user chooses an accumulator that is not capable of maintaining the pressure, it may cause premature failure.
To prevent leakage, a pilot-operated check valve should be installed. The check-valve should be closed when the accumulator is not in use.